In November 2016, a new version of the EN388 standard – used to regulate cut protection in safety gloves – was published and came into effect from 1 April 2019.
Importing and manufacture against the old EN 388 standard stopped from April 2019. However, products tested against the old coupe test EN 388:2003 may still be available in the marketplace after this date but as of the start of 2023, they are no longer valid.
Here is a summary of the key changes. There have been no major technical changes to the testing methods for tear or puncture resistance.
Abrasion | Cut Protection (Coupe Test) | Cut Protection (TDM Test) | Impact Protection Testing (if relevant) | Marking |
The abrasion resistance test uses 180 grit abrasive material (instead of 100 grit as specified in the 2003 version). As a result, some abrasion scores may change when a product is recertified under the new test conditions. | The number of test cycles of the circular blade is now limited to a maximum of 60 cycles, whether the blade has cut though the fabric or not. In the event that the blade becomes blunt or 60 rotations are performed without cutting through the material sample or the test is simply not taken, then the TDM Test will be conducted and an “X” will be displayed as the second digit. Manufacturers may choose to opt out of the coupe test and only submit their product for the TDM Test. | The TDM test measures the amount of force applied to a straight blade to cut through the material with a single 20mm stroke. This resistance is noted by the letters A to F as the 5th digit. | The EN 13594:2015 test method has been introduced. Gloves which meet the test criteria will be marked with a ‘P as the 6th digit’. | The gloves’ markings have been expanded to display the results from TDM cut test and the optional impact protection test. These are shown below. |
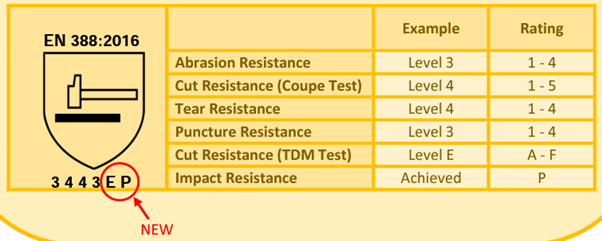
UNDERSTANDING EN 388: 2016: A Revised Standard for Gloves Giving Protection from Mechanical Risks
Safety professionals are constantly trying to find new ways to keep workers better protected and reduce injuries in the workplace. The latest figures released by HSE show that 441,000 Workers sustaining a non-fatal injury in the UK last year. General-purpose protective gloves account for the largest market share of all personal protective equipment (PPE) sold so it’s crucial to strive for continuous improvement in this area.
In November 2016, a new version of the EN 388 standard – used to regulate cut protection in safety gloves – was published. This paper outlines the key changes to the EN 388 Standard.
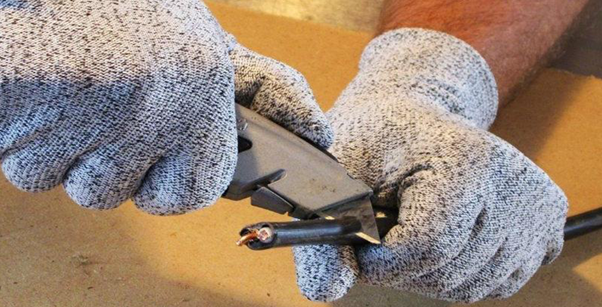
EN 388 is the recognised global standard that determines a glove’s performance against mechanical hazards. The standard uses index values to indicate the performance levels for safety gloves in protecting the user against numerous mechanical risks such as abrasion, blade cut, tear, puncture and impact. It also specifies the testing and marking required for protective gloves.
ABRASION |
The type of abrasive paper used in the test has been changed. The 100 grit materiel has been increased to 180 grit material. This means that some abrasion scores, may change when tested to the new standard. To measure the abrasion resistance of a glove, the glove material is fitted to a Martindale abrasion machine and the rubbing head moves over the test material in an elliptical motion over a table covered with 180 grit abrasive material. The number of cycles required to make a hole in the test material relate to the 1-4 levels of abrasion performance |

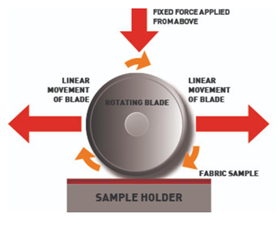
CUT PROTECTION (Coupe Test)
Up until now, the ‘Coupe Blade Cut Test’ has been the standard test method for cut protection. A rotating circular blade moves horizontally to-and-fro across a fabric sample with a fixed force of 5 Newtons (N) applied from above. The test ends when the blade breaks through the sample material and the result is calculated as an index value. This result is determined by the cycle count needed to cut through the sample and additionally by calculating the degree of wear and tear on the blade.
In the 2016 update, the Coupe Test method has been revised which sees the number of test cycles limited to 60 (from 80) whether or not the blade has cut through the fabric. This means that some gloves may not score so well in the restricted number of cycles. The number of cycles of the rotating blade is used to determine the cut index. The performance is shown on the glove as a number.

High performance fibres and materials (such as fibreglass or steel) are used to achieve greater levels of cut protection in safety gloves. These blends are designed to protect against sharps that can damage the hand. Equally, due to their robust nature, they can also blunt the blades of the test machine used to test for protection ratings. The standards committee felt that because blunting of the blade can occur in the coupe test; this particular method is no longer representative of the actual degree of protection provided by the glove. Manufacturers may choose not to take the Coupe Test or not declare the result for a number of reasons. The glove may not perform as well in the reduced number of cycles or the cost to perform two cut tests is prohibitive. In this instance an “X” may be displayed in the place of a Coupe Test result shown as a second digit under the EN 388 pictogram.
CUT PROTECTION (EN ISO 13997:1999 / TDM Test)
In instances where blunting of the coupe test blade occurs, an additional test is being introduced, the EN ISO 13997:1999 cut test – or TDM or Knife Test. The TDM Test is designed to better simulate real-world situations such as an accidental cut or slash.
The objective of this new cut protection test is to determine the resistance of the safety glove by applying the sample fabric with calculated force in a single movement. Using a straight blade in testing, this new method measures the average load required to achieve a cut after the blade has travelled once over a 20 mm distance. Performance levels are measured in Newtons and grams indicated by a six-letter classification system.
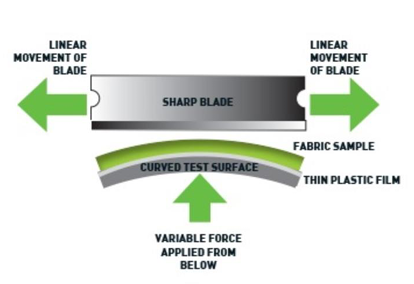
Because the blade only travels once over the specimen and each blade is only used once, the problem of blunting blades with repeated cycles is eliminated. The TDM performance level result is added as a 5th digit under the EN 388 pictogram.

The introduction of this new cut test will enable safety managers to better match the protection required against the hazards encountered by the workforce. (If you were wondering, TDM stands for Tododynamometer – the device used to measure cut resistance.)
FAQs
- Are the Coupe and TDM tests the same? No, these tests are fundamentally different tests. The coupe test uses a rotating circular blade moving backwards and forwards over the fabric with a fixed force. The TDM test measures a single straight blade cut with variable weighted pressure with the blade replaced each time so no dulling of the blade occurs.
- Can you correlate results from the 2 tests? No, these tests are not the same and cannot be correlated. More important is the risk assessment for the user and the level of protection required.
- Is the New TDM Test better than the Coupe Test? No. They measure different types of cut and serve a different purpose.
- Do manufacturers need to take both tests? No. Until 2023, manufacturers can choose to submit or only display the results from the TDM Test. If they know their material will blunt the blade, the performance level may decline due to the reduced number of rotations (just 60) or there may be cost restrictions to perform two tests, the Coupe test is optional and the TDM test is mandatory. If the rotary blade retains its sharpness, then the Coupe Test must be used and the TDM test becomes optional. Ask the manufacturer why they did not publish their Coupe Test results if an “X” is displayed for either test.
IMPACT RESISTANCE
A new addition within the EN 388:2016 standard is an optional test to measure the impact protection of a glove that claims to have impact resistance properties, usually added to the back of the hand and / or the knuckles. The test is carried out in accordance with EN 13594:2015 6.9 Protective Gloves for Motorcycle Riders. The area/material of impact protection is tested by being secured to a domed anvil and impacted with a 2.5 kg flat face striker and energy of 5 J. Gloves must meet the requirement of level 1 of EN 13594:2015 – the mean transmitted force shall be ≤ 7.0 kN with no single results greater than ≤ 9.0 kN. If the glove meets this requirement, a “P” is added as the last digit to the EN 388:2016 glove marking.
MARKING
The pictogram will not change, however, when a glove has been tested to the EN 388:2016 standard you can understand the new marking as shown below
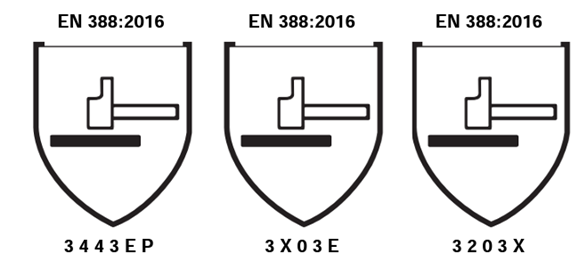
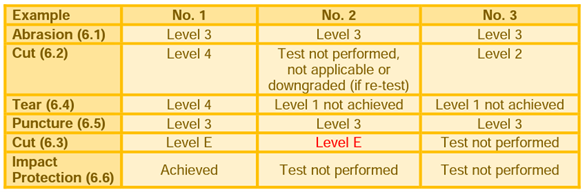
Note: If tests are not performed or are not applicable, “X” will be placed instead of a number/letter. Please note that until 2023, products tested by the old coupe test EN 388:2003 are still valid. Although importing and manufacture against this standard stopped in April 2019, older products with the 2003 marking may still be available in the market place.
WHAT THE CHANGES MEAN FOR USERS
This change only affects new products being certified. All pre-existing EN 388 certifications continue to be valid for a maximum of 5 years until new certification is necessary. Using both the coupe and TDM tests, products with higher levels of cut protection can be identified. As a guideline, these are summarised in the table below.
STAY INFORMED
Keep yourself informed and compliant through PWS’s Knowledge Hub. Through this regularly updated resource, we aim to keep you updated with legislation, H&S information and white papers like this one.
To request a FREE hand protection risk assessment or try out a FREE sample of one of our Cut Resistant Gloves or Sleeves, please contact us.